Discover What is Porosity in Welding and Its Impact on Architectural Stability
Discover What is Porosity in Welding and Its Impact on Architectural Stability
Blog Article
Porosity in Welding: Identifying Common Issues and Implementing Best Practices for Prevention
Porosity in welding is a prevalent problem that typically goes unnoticed until it creates considerable issues with the stability of welds. In this conversation, we will certainly check out the vital factors contributing to porosity formation, analyze its destructive effects on weld efficiency, and go over the ideal practices that can be embraced to reduce porosity incident in welding processes.
Common Sources Of Porosity

Another regular culprit behind porosity is the existence of impurities externally of the base steel, such as oil, oil, or rust. When these pollutants are not properly gotten rid of prior to welding, they can evaporate and become entraped in the weld, causing problems. In addition, using filthy or damp filler products can introduce impurities into the weld, contributing to porosity issues. To mitigate these common root causes of porosity, extensive cleaning of base metals, proper securing gas option, and adherence to ideal welding parameters are important techniques in achieving top quality, porosity-free welds.
Effect of Porosity on Weld Top Quality

The existence of porosity in welding can substantially endanger the architectural stability and mechanical buildings of bonded joints. Porosity develops gaps within the weld steel, deteriorating its general stamina and load-bearing capability.
One of the primary consequences of porosity is a decrease in the weld's ductility and strength. Welds with high porosity levels tend to show reduced impact stamina and reduced capability to deform plastically before fracturing. This can be specifically worrying in applications where the bonded elements undergo vibrant or cyclic loading problems. Porosity can hamper the weld's capability to effectively send pressures, leading to premature weld failing and prospective safety threats in important structures. What is Porosity.
Best Practices for Porosity Avoidance
To boost the structural integrity and quality of bonded joints, what certain steps can be applied to decrease the event of porosity during the welding procedure? Porosity prevention in welding is essential to make certain the integrity and stamina of the final weld. One efficient technique is correct cleansing of the base steel, eliminating any kind of pollutants such as corrosion, oil, paint, or moisture that might bring about gas entrapment. Making sure that the welding tools is in great condition, with tidy consumables and appropriate gas flow prices, can additionally considerably lower porosity. Additionally, preserving a steady arc and click reference regulating the welding parameters, such as voltage, present, and take a trip rate, aids create a constant weld swimming pool that minimizes the threat of gas entrapment. Making use of the right welding method for the specific product being bonded, such as changing the welding angle and gun position, can even more stop porosity. Normal examination of welds and immediate remediation of any type of problems determined during the welding process are crucial techniques to stop porosity and produce high-quality welds.
Significance of Correct Welding Methods
Applying proper welding techniques is paramount in making sure the architectural integrity and top quality of welded joints, developing upon the structure of efficient porosity avoidance steps. Too much warmth can lead to enhanced porosity due to the entrapment of gases in the weld pool. In addition, utilizing the suitable welding specifications, such as voltage, present, and travel speed, is essential for achieving sound welds with marginal porosity.
Furthermore, the selection of welding procedure, whether it be MIG, TIG, or stick welding, must line up with the particular requirements wikipedia reference of the project to make certain optimum results. Correct cleansing and preparation of the base metal, in addition to selecting the appropriate filler material, are also important parts of competent welding methods. By sticking to these ideal practices, welders can minimize the risk of porosity formation and create high-quality, structurally sound welds.
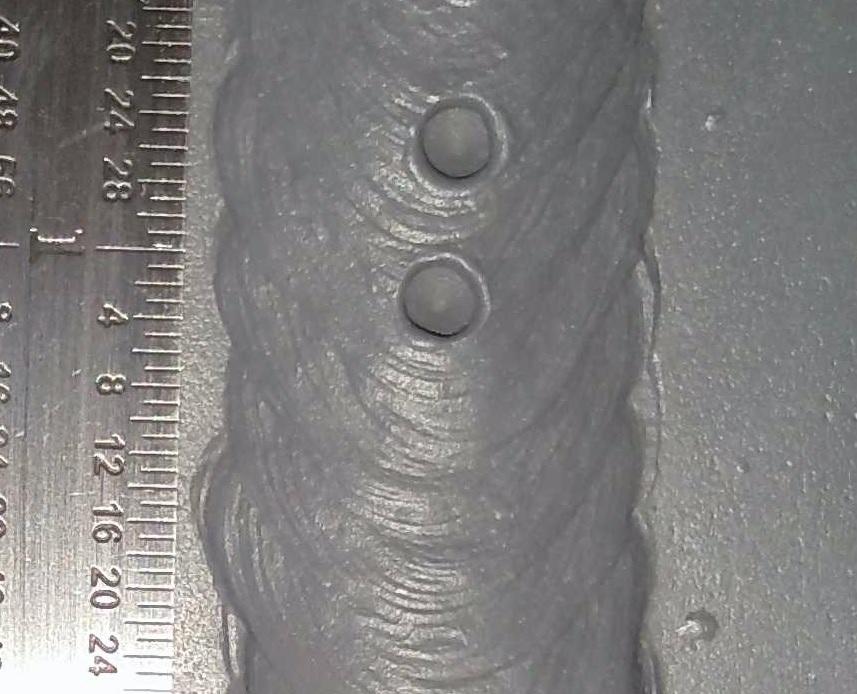
Evaluating and Quality Assurance Actions
Quality control steps play a critical role in verifying the integrity and dependability of Website welded joints. Checking treatments are vital to find and protect against porosity in welding, ensuring the strength and sturdiness of the last item. Non-destructive screening techniques such as ultrasonic screening, radiographic screening, and visual assessment are frequently utilized to determine prospective flaws like porosity. These methods permit the assessment of weld top quality without endangering the integrity of the joint. What is Porosity.
Post-weld evaluations, on the various other hand, assess the last weld for any type of problems, including porosity, and validate that it meets specified standards. Executing a thorough quality control plan that consists of thorough testing procedures and assessments is paramount to decreasing porosity concerns and making sure the total quality of welded joints.
Final Thought
To conclude, porosity in welding can be an usual issue that influences the quality of welds. By determining the typical sources of porosity and carrying out ideal practices for prevention, such as proper welding techniques and testing steps, welders can make sure top quality and reputable welds. It is vital to focus on avoidance methods to reduce the incident of porosity and preserve the stability of bonded frameworks.
Report this page